When to Call in Packaging Equipment Repair Services for Maximum Efficiency
When to Call in Packaging Equipment Repair Services for Maximum Efficiency
Blog Article
Comprehend the Benefits of Utilizing Specialist Product Packaging Tools Repair Work Solutions
Making use of professional product packaging tools repair solutions provides a number of vital advantages for services. Improved devices long life and boosted operational effectiveness are remarkable advantages. Knowledgeable technicians can rapidly attend to concerns, preventing small troubles from rising into significant downtime. Furthermore, routine maintenance supports conformity with market criteria, guaranteeing security and securing brand online reputation. Comprehending just how these aspects contribute to total productivity is essential for any company aiming to optimize its procedures. What effects does this have for future growth?
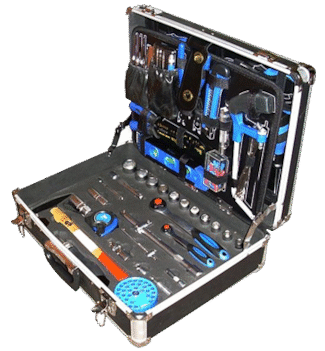
Improved Devices Durability
Proper upkeep through specialist product packaging tools repair work solutions significantly adds to improved devices longevity. By addressing wear and tear without delay, these services help avoid minor problems from rising right into major break downs. Skilled professionals have the requisite knowledge and proficiency to identify potential problems that may not appear to untrained personnel. Routine inspections and timely repair services ensure that machinery runs within excellent criteria, reducing the risk of catastrophic failures.Moreover, professional fixing solutions commonly use top quality substitute parts, which can considerably expand the life expectancy of equipment. This positive strategy not only decreases downtime but likewise cultivates a consistent manufacturing circulation. Services that purchase expert upkeep are likely to see a much more trustworthy efficiency from their product packaging equipment, inevitably bring about reduced expenses related to frequent substitutes. Essentially, the longevity of product packaging machinery is directly influenced by the dedication to expert and routine repair service services.
Enhanced Operational Efficiency
Buying specialist packaging tools repair service services straight enhances operational effectiveness (Packaging Equipment Repair Services). Professional service technicians possess specialized expertise and abilities, permitting them to identify and solve problems quickly, lessening downtime. By guaranteeing that devices operates at peak performance, businesses can maintain constant manufacturing routines, thereby satisfying consumer demands more effectively.Furthermore, regular maintenance and timely fixings prevent minor issues from intensifying into substantial failures, which can interfere with process and bring about costly delays. With professionally repaired tools, staff members can focus on their core jobs instead of fixing malfunctioning machines.The integrity of well-maintained packaging equipment adds to smoother operations, allowing business to enhance their production processes. Inevitably, this proactive strategy not only enhances operations however likewise promotes a much more effective workplace, allowing services to adapt to changing market requires with better dexterity. Improved functional effectiveness becomes a keystone for sustained growth and competition in the product packaging market
Cost Financial Savings on Repair Works
Implementing professional packaging tools repair service solutions can lead to significant expense financial savings for organizations. By dealing with fixing needs quickly and successfully, companies can stay clear of the high prices connected with extended tools downtime. Hold-ups out of commission equipment can lead to shed production, which directly affects earnings. In addition, professional repair services often supply bulk or regular upkeep, lowering the probability of significant breakdowns in the future.In addition, using specialized solutions can prolong the life expectancy of equipment, minimizing the need for costly substitutes. Organizations can likewise gain from foreseeable repair work prices, enabling for better budgeting and financial preparation. In addition, contracting out repair work can maximize interior sources, enabling personnel to concentrate on core operations rather than repairing devices concerns. Overall, specialist product packaging equipment repair solutions supply a critical approach to taking care of fixing expenses, eventually improving a company's lower line while making certain functional continuity.
Accessibility to Specialist Understanding and Abilities
While companies may have skilled team, depending on expert packaging equipment repair service services supplies access to a broader series of professional expertise and specialized abilities. These specialists are commonly educated in the latest innovations and market criteria, which enables them to resolve complex issues that internal groups could not be geared up to manage. Their experience extends numerous tools kinds and brand names, allowing them to promptly detect problems and carry out efficient solutions.Moreover, specialist repair service technicians stay upgraded on innovations and best methods, guaranteeing that repair services are performed effectively and properly. This degree of know-how can lead to improved devices longevity and efficiency, eventually profiting the firm's lower line. By using these specialized solutions, companies can take advantage of a wealth of expertise that enhances their functional capabilities without the need for comprehensive internal training or financial investment in additional resources. This strategic method helps preserve the honesty of packaging procedures while optimizing source appropriation.
Reduction of Downtime
Minimizing downtime is crucial for keeping functional effectiveness in product packaging centers. Quick action times, coupled with professional troubleshooting abilities, enable technicians to attend to concerns quickly. Additionally, reliable repair processes assure that equipment is restored to come to a head efficiency with minimal disturbance.
Quick Feedback Time
A speedy action time is vital for organizations relying upon product packaging devices, as also small hold-ups can lead to significant functional interruptions. When tools malfunctions, timely attention from professional repair solutions can dramatically reduce downtime, permitting production schedules to return to promptly. Quick response times not just reduce the influence on total performance however also help keep client contentment by conference delivery timelines. Specialist fixing services typically focus on immediate demands, making sure that professionals are available to deal with problems as they emerge. This level of responsiveness is vital in affordable sectors where performance is extremely important. Inevitably, companies profit from a reliable collaboration with repair solutions that recognize the seriousness of their operational requirements, promoting a positive approach to tools upkeep and management.
Professional Troubleshooting Abilities
Specialist troubleshooting abilities are vital for lessening downtime in packaging operations. Knowledgeable specialists possess the capacity to promptly identify the source of equipment breakdowns, which is essential in keeping functional performance. They use their extensive understanding and experience to diagnose concerns properly, making certain that prospective problems are addressed before they rise. This positive technique minimizes the danger of prolonged outages and boosts efficiency. Additionally, professional troubleshooters can carry out targeted options that stop recurring concerns, causing a much more trustworthy product packaging process. Their know-how not just find more information conserves time but likewise decreases the financial impact of unexpected failures. In an industry where time is cash, having access to efficient troubleshooting skills is a vital asset for any product packaging operation.
Effective Repair Processes
Effective fixing processes play a vital role in minimizing downtime for packaging devices. Quick diagnosis and efficient execution are vital elements that make it possible for service technicians to determine issues swiftly and implement services without unneeded hold-ups. Professional repair service services often utilize advanced devices and technologies, enabling for even more precise repair work and reducing the likelihood of reoccuring issues. Moreover, standard procedures and structured operations enhance the repair service procedure, making certain that fixings are finished regularly and efficiently. This efficiency not just recovers devices performance however likewise improves overall operational performance. By spending in specialist fixing solutions, organizations can greatly reduce the moment equipment stays idle, inevitably resulting in improved profitability and functional dependability in their packaging processes.
Compliance With Industry Criteria
Compliance with market requirements is vital for guaranteeing the stability and security of packaging devices. Following regulatory requirements and tools security criteria not only secures employees however likewise improves functional efficiency. Implementing market ideal techniques is essential for maintaining compliance and fostering a society of safety and security and top quality within companies.
Governing Compliance Guarantee
Making certain regulatory conformity in packaging devices repair service is important for keeping industry standards and guarding item stability. Expert repair service services are well-versed in the specific laws controling product packaging processes, guaranteeing that all repair services fulfill the essential lawful needs. This expertise lessens the risk of non-compliance, which can bring about costly penalties and interruptions in manufacturing. In addition, adherence to governing requirements aids in maintaining brand name track record and consumer trust fund. By utilizing specialized repair work solutions, firms can improve their procedures while making certain that their tools runs within the structure of sector policies. This positive method not only improves operational effectiveness but also reinforces dedication to high quality and security in the product packaging sector.
Devices Safety Criteria
While many firms focus on performance in their packaging operations, adherence to equipment safety requirements is necessary for stopping mishaps and guaranteeing a secure workplace. Compliance with these requirements helps minimize dangers connected with equipment use, shielding both possessions and staff members. Expert packaging tools repair service solutions play an essential duty in keeping security by ensuring that makers are regularly inspected, serviced, and updated according to market guidelines. This aggressive strategy not just boosts operational reliability but likewise promotes a society of safety and security within the work environment. By buying specialist repair work services, business can accomplish conformity with safety and security standards, decrease liability threats, and ultimately advertise a much safer, more productive atmosphere for their labor force.
Market Best Practices
Sticking to industry best practices is crucial for product packaging firms intending to preserve functional quality and regulatory compliance. Compliance with sector criteria not just improves product quality yet additionally decreases risks connected with equipment breakdowns and safety and security dangers. Regular training and certification for specialists ensure that they are well-versed in the most recent repair work techniques and safety methods. Additionally, routine maintenance schedules aid in recognizing potential concerns look at this website prior to they escalate, thus prolonging devices life. Making use of standard treatments and documentation techniques assists in consistency and liability. By accepting these ideal methods, product packaging companies can boost effectiveness, reduce downtime, and promote a society of security and reliability, inevitably bring about boosted consumer complete satisfaction and commitment.
Raised Safety in the Office
As business prioritize the health and safety and security of their workers, the duty of professional product packaging equipment repair work services comes to be progressively important in boosting workplace security. Well-kept equipment greatly decreases the threat of mishaps, injuries, and tools breakdowns. Professional professionals possess the experience to recognize possible risks and execute needed repairs quickly, guaranteeing that equipment operates within risk-free parameters.Regular examinations and upkeep by official statement certified professionals also reduce the possibilities of unanticipated failures, which can result in hazardous scenarios on the manufacturing floor. By using these solutions, firms foster a society of safety and security that prioritizes employee wellness. In addition, compliant and upgraded tools sustains adherence to market guidelines, decreasing lawful dangers connected with office security violations - Packaging Equipment Repair Services.Ultimately, investing in expert packaging tools fixing solutions not only safeguards employees but also improves operational efficiency, resulting in an extra productive workplace atmosphere
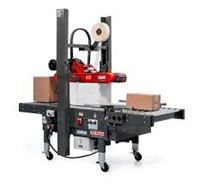
Often Asked Concerns
Just how Do I Pick the Right Product Packaging Devices Fixing Service?
Selecting the appropriate packaging devices repair work solution entails reviewing proficiency, client testimonials, action times, and guarantee options. In addition, examining the service's familiarity with certain tools and availability of components can greatly influence the decision-making process.
What Kinds of Packaging Tools Can Be Repaired Expertly?
Different sorts of packaging devices can be repaired expertly, including filling up devices, classifying devices, securing machines, and palletizers. Each type calls for specialized knowledge to guarantee effective repair work and optimum operational effectiveness in product packaging processes.
Just how Typically Should I Schedule Upkeep for My Product Packaging Tools?
Setting up maintenance for packaging devices must occur every 3 to 6 months, depending upon use intensity and supplier recommendations. Routine upkeep guarantees peak efficiency, extends devices life expectancy, and reduces unexpected malfunctions that could interfere with operations.
Exist Service Warranties on Repair Works Offered by These Solutions?
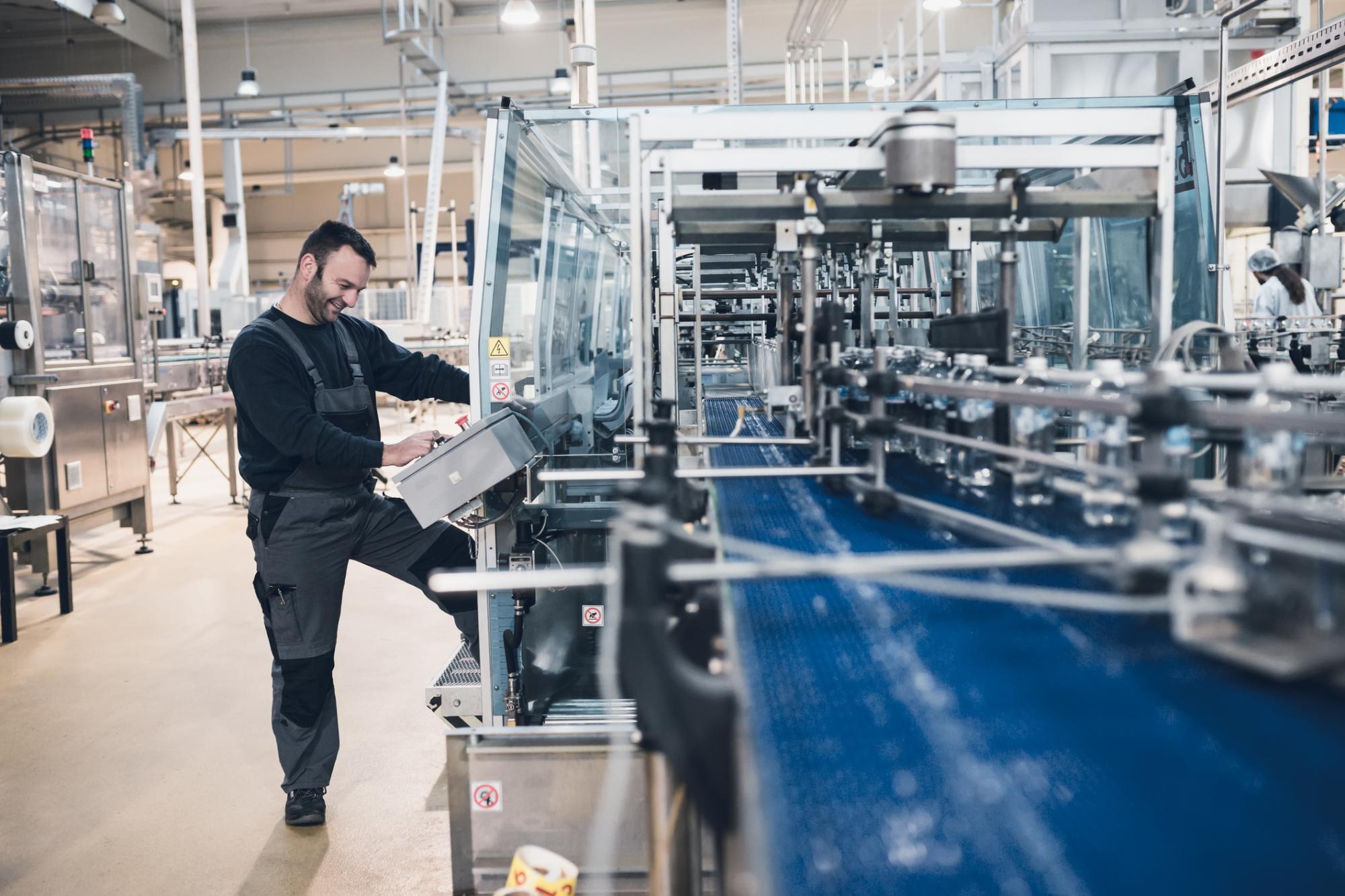
What Should I Do if My Equipment Breaks Down All Of A Sudden?
When tools breaks down all of a sudden, it is recommended to examine the concern, guarantee safety, speak with the guidebook for repairing tips, and speak to a qualified service technician for professional support to reduce downtime and warranty reliable repairs. Proper upkeep with specialist packaging equipment fixing solutions significantly adds to improved devices long life. Normal evaluations and timely repair services guarantee that equipment operates within suitable parameters, lowering the danger of disastrous failures.Moreover, professional fixing solutions typically utilize top quality substitute components, which can greatly prolong the lifespan of devices. With skillfully fixed tools, staff members can concentrate on their core jobs instead than fixing malfunctioning machines.The integrity of well-kept product packaging equipment contributes to smoother operations, making it possible for companies to optimize their manufacturing processes. Their experience extends numerous equipment kinds and brand names, permitting them to rapidly diagnose troubles and carry out effective solutions.Moreover, specialist repair service service technicians stay upgraded on technologies and ideal techniques, ensuring that repair work are performed efficiently and properly. Properly maintained equipment considerably lowers the threat of accidents, injuries, and equipment breakdowns.
Report this page